Pack and Ship Guide
In this guide we will be showing you how to set up the Pack and Ship feature of our
Multi Carrier app.
You will learn how to do this for the Order and Order Products objects (Multi-Carrier also supports custom
objects).
Prerequisites
Before you follow the guide, please ensure you have completed the following prerequisites:
- Installed the Multi-carrier app
- Created a preference with your live credentials or test credentials
- Created a lookup relationship to the object that you would like to ship to
Prepare related objects
In order for Pick and Pack to function properly, you will need to setup your related objects - mainly order lines and products.
Add a barcode field to the Product Object
This can be a text field, such as the following:
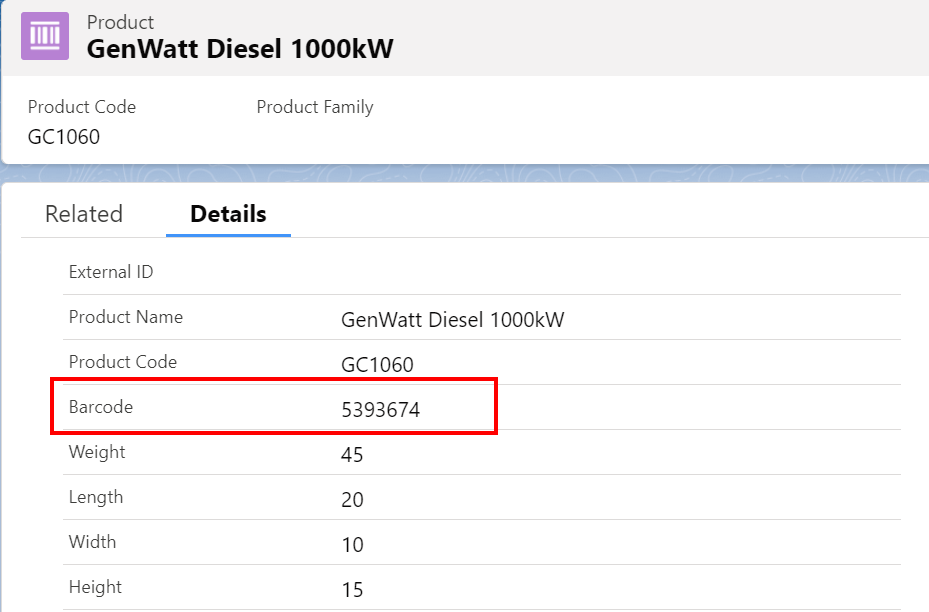
Add field "Quantity Packed" to the Product Line Object
As you are preparing orders, this field will store how many products have already been packed and shipped:
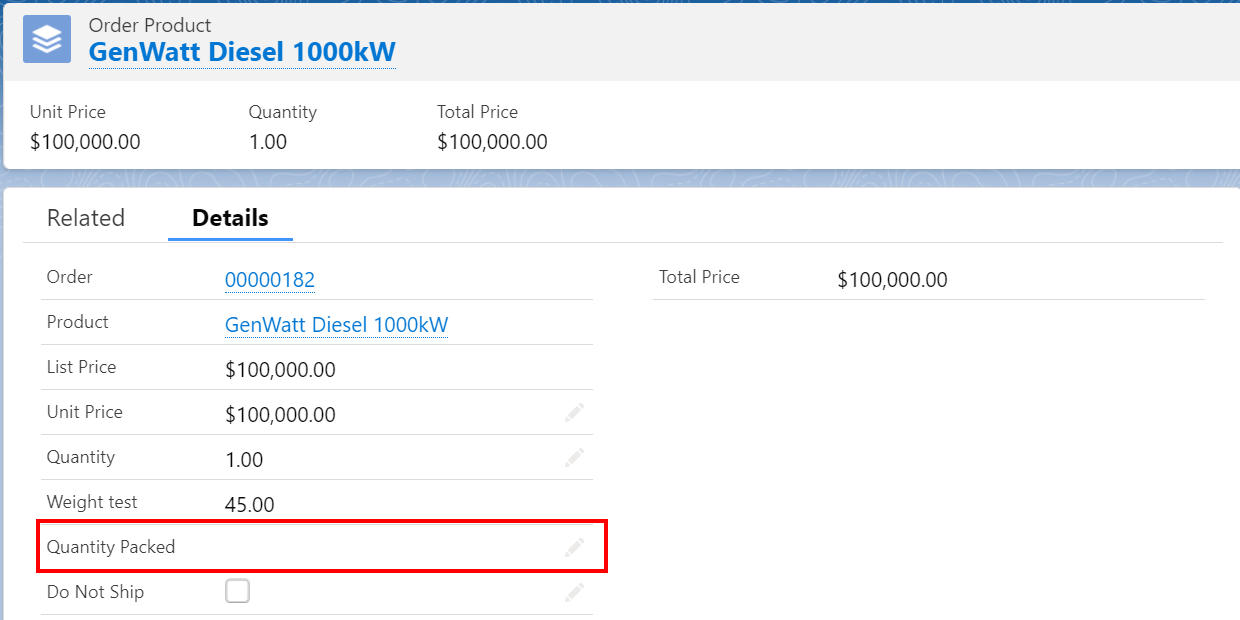
Create the lookup from our Customs Items Object to the Order Product object.
This relationship allows you to track which products (and how many) went into each package.
Go to Setup > Object Manager and find the Customs Items object (above v1.108 the Product object)

and click on New.
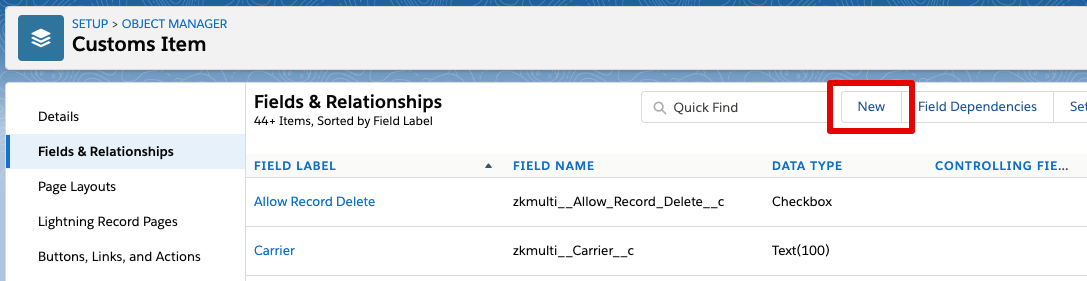
Choose the Lookup Relationship:
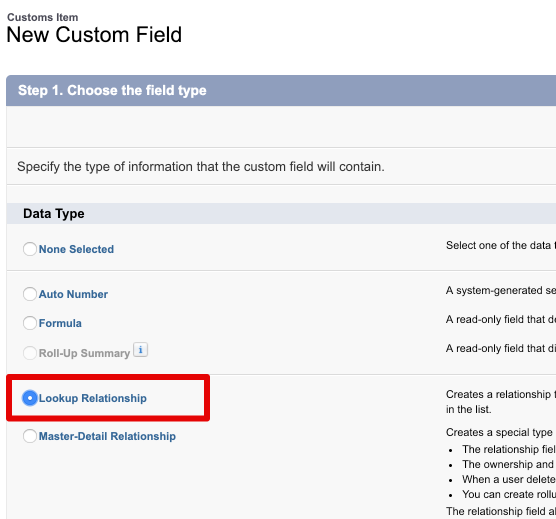
Then choose your child object, in this guide we are using the Order Product object:
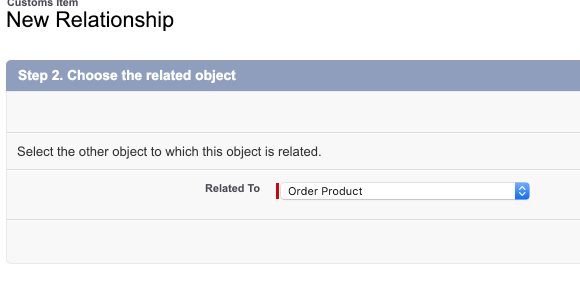
Then click through until you are able to save.
Create Custom Address Source
The next step is to create a custom address source. You can follow our guide to creating the Custom Address Source if you haven't done it before by following this link. Below you will find the fields needed for Pick and Pack specifically.
Recipient fields
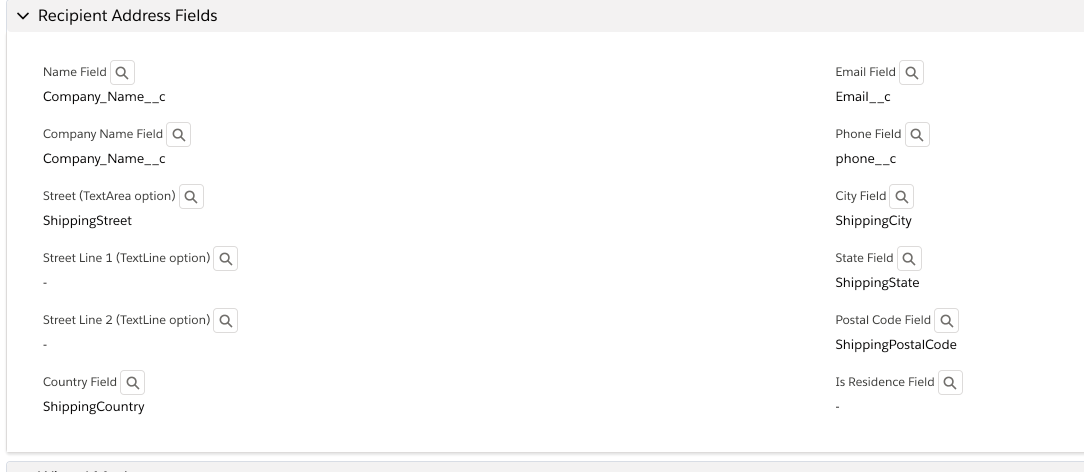
Ensure that you have set the Service Type and Packaging Type.
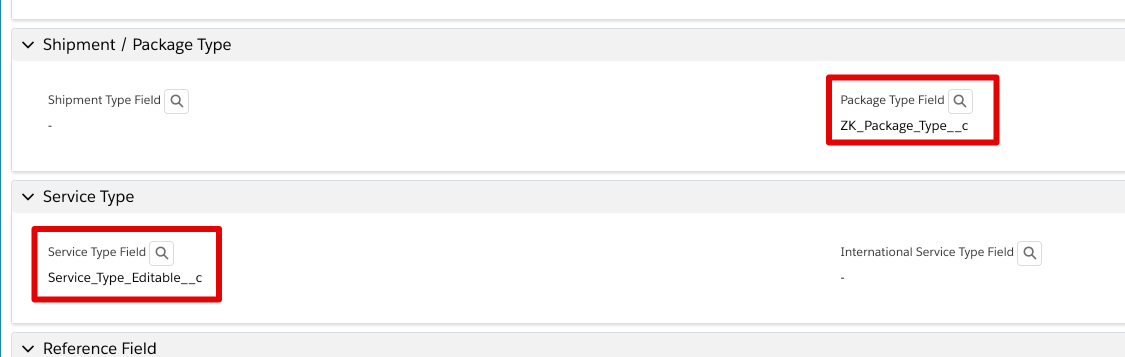
Be sure to set Wizard Mode to Pick and Pack:

And finally you will also need to pull product data into the Pick and Pack system using the "Products / Customs Items" section:
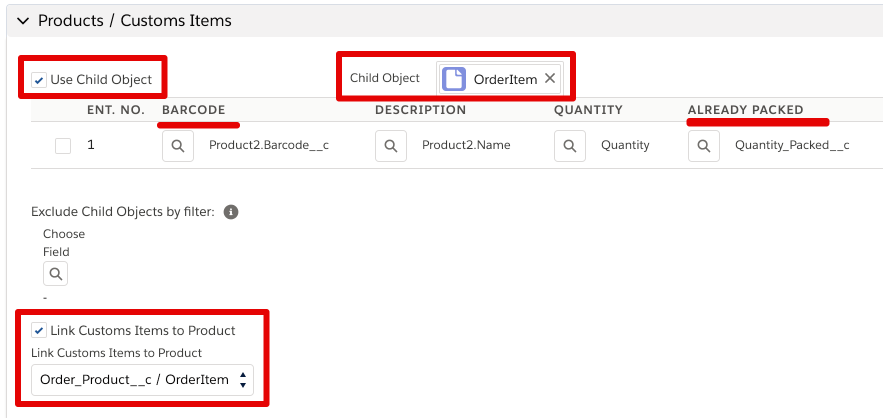
Here is an explanation of the highlighted items above.
Use Child Objects:
You need to Use Child Objects so that we can get all the items that need to be packaged.
Child Object:
Choose the Child Object that holds your packing data. In our case its the OrderItem.
Barcode:
If you set this, then you will see the Barcode field appear on your Pick and Pack page so that you can scan your items with a barcode reader.
Already Packed:
This is the newly created field that you set up in Step 1, and holds the information as to how many items still need to be packed.
Link Customs Items to Product:
This is the Lookup that you created from the Customs Item to your Order Product object. Once your shipment is created, the Customs Items related list is linked to your product line.
Create Custom Address Source for Outbound and Return
If you want to create a return label at the same time as creating an outbound label then you need to create 2 Custom Address Sources. One for outbound and one for return.
Here are the steps to setting this up:
- Create an Outbound Custom Address source by following this link
- Create a return Custom Address source and set the fields as you did in step 1, but for the shipment
type please enter a static value of: RETURN
- Go back to your outbound Custom Address source you did in step 1 and click on edit. Change the
Wizard Mode to be Outbound and Return (Pick and Pack):
Which then allows you to set the Return Custom Address source that you set up in step 2. - The last step is to set the Origin Custom Address Source Id to a static value like so in your Return
Custom Address Source:
You can get this value by going to your Outbound Custom Address Source and copying the 15/18 characters of the Salesforce Object ID found in the browser.
Set up Containers
Next you need to set up your Containers under the Packages object.
You can find the detailed steps on this in our Packages guide.
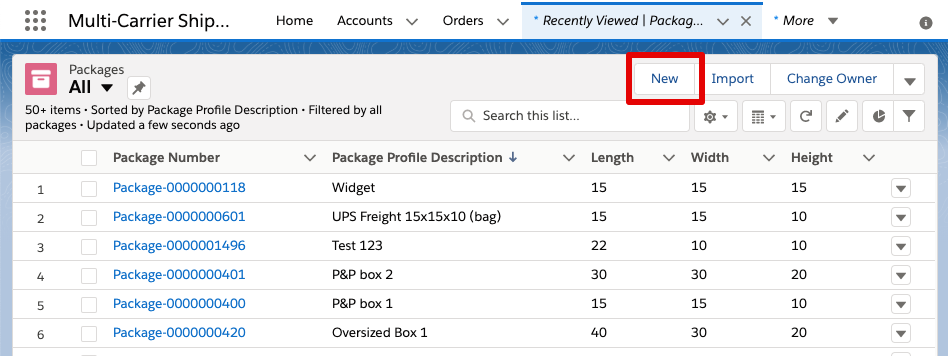
Packages must be created for each carrier.
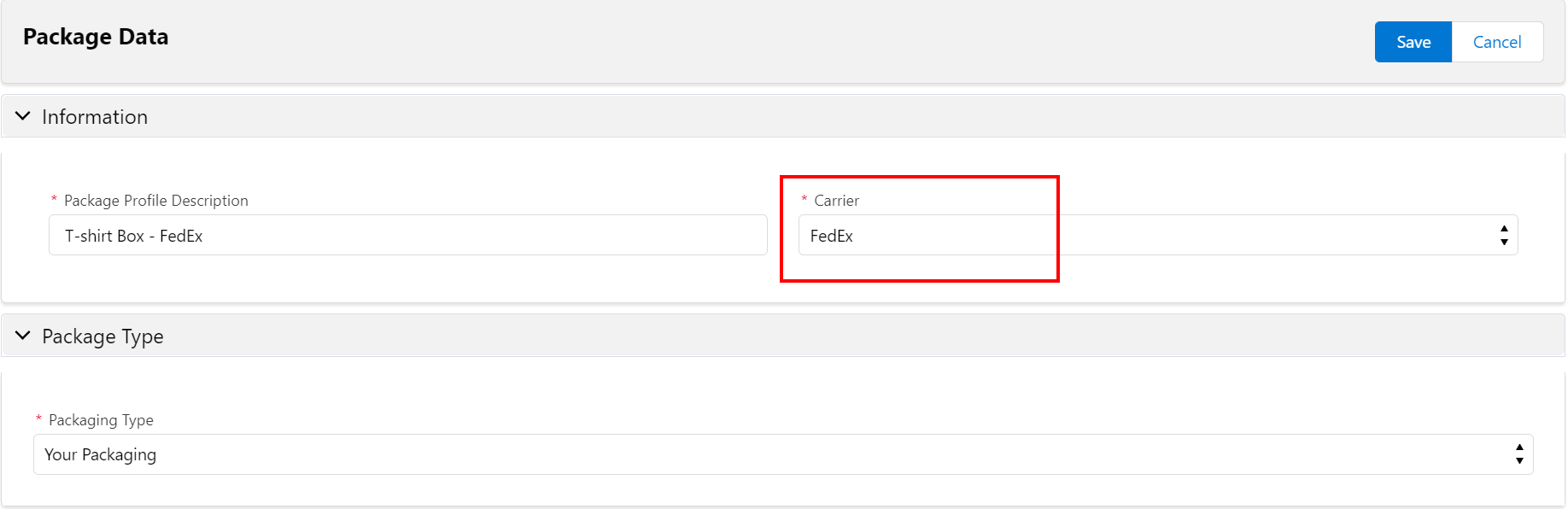
Don't forget to set the Quantity to 1. You can leave the Weight and Declared Value to be 0 as these get set on the Pick and Pack team.
Additional Settings
You can set up validations or limitations and additional settings on the pick and pack shipping.
Block Partial Shipments
It is possible to block partial shipments, meaning only packing a few items or no items at all. Go to the custom address source and scroll down to Enhance Functionality Settings.
Add a new row and select All Carriers: Pick and Pack: Disable Partial Shipments. Set it to TRUE.

If not all items are packed when hitting "Ship" the following error message will appear:

Auto-calculate total package weight
It is possible to automatically calculate the total weight of each package based on the items packed. Go to the custom address source and scroll down to Enhance Functionality Settings.
Add a new row and select All Carriers: Pick and Pack: Auto Calculate Weight Total. Set it to TRUE.

When you click Pack or Pack All the weight will be automatically calculated.
Auto-calculate total package value
It is possible to automatically calculate the total value of each package based on the items packed. Go to the custom address source and scroll down to Enhance Functionality Settings.
Add a new row and select All Carriers: Pick and Pack: Auto Calculate Value Total. Set it to TRUE.

When you click Pack or Pack All the value will be automatically calculated.
Modify return containers
Unless this setting is enabled the return packages will be replicated based on the outbound packages. If you enable this option you can modify the return packages in the wizard. Go to the custom address source and scroll down to Enhance Functionality Settings.
Add a new row and select All Carriers: Pick and Pack: Modify Return Containers / Products. Set it to TRUE.

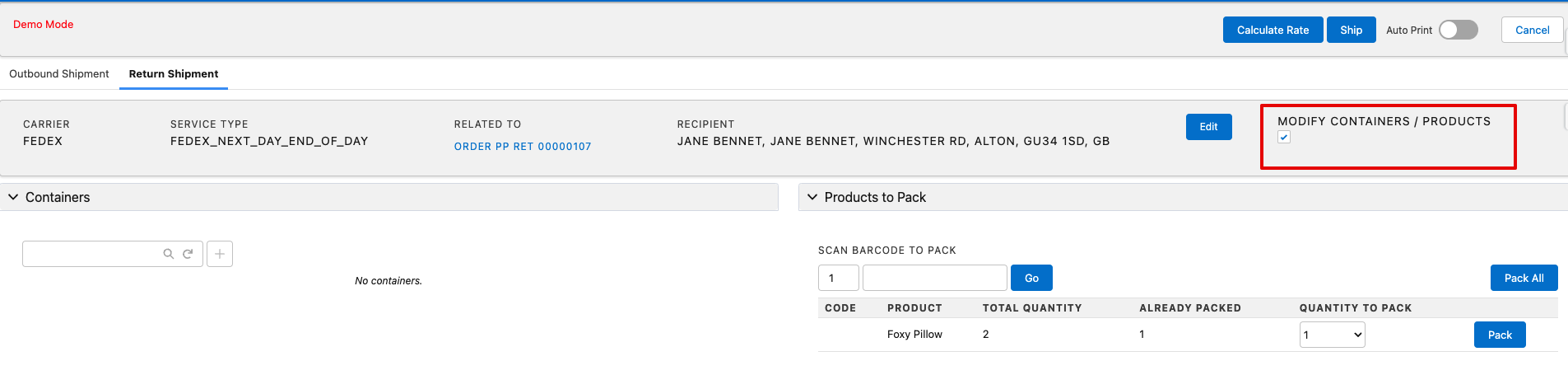
Test and Start Shipping
Once you have done the above steps, you should now be able to go to your Order object and click on New Shipment, and you should now see this a screen like so:
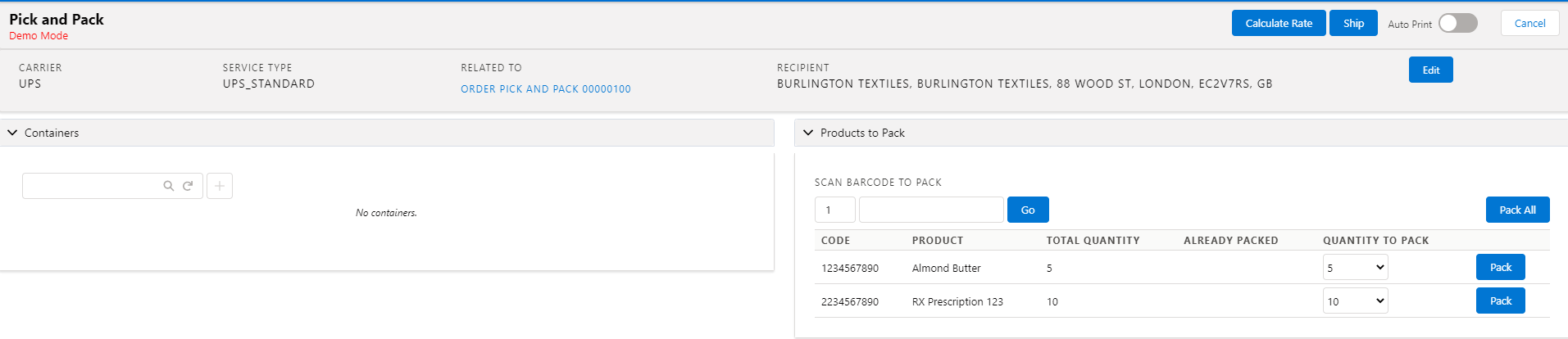
The first thing you need to do is select a Container, you do this by selecting the containers input box, and your containers should then appear as a list. If you have lots of boxes you can search for them by name.
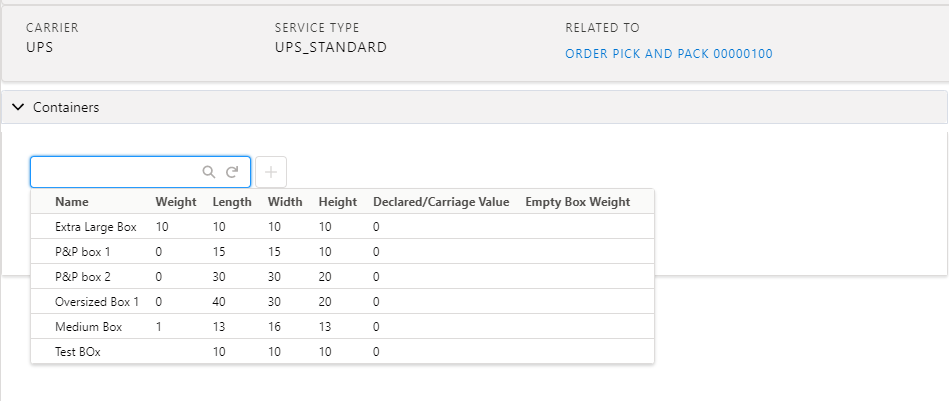
Once you have your container selected you can start to pack your items by selecting the Quantity to Pack and clicking on the Pack button.

Each time you pack an item it will be show on the left hand side under your active container.

If you need to add another container, just use the container box again to add a new container.
You can only have 1 container active at a time, so you can select which container is active using the toggle as you see here
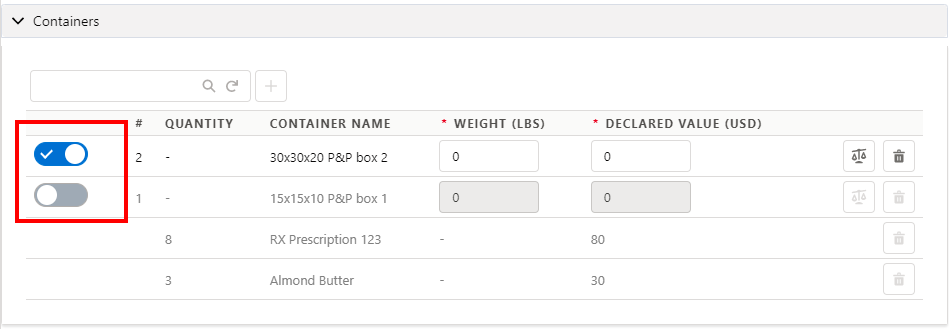
Once you have your newly activated empty container, pack some more products into it:
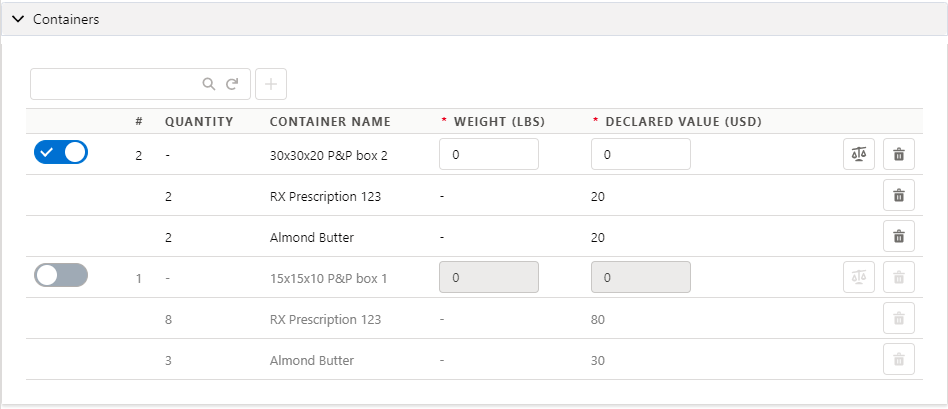
Once you have finished packing all of a particular product you will see that it's no longer available to be packed.
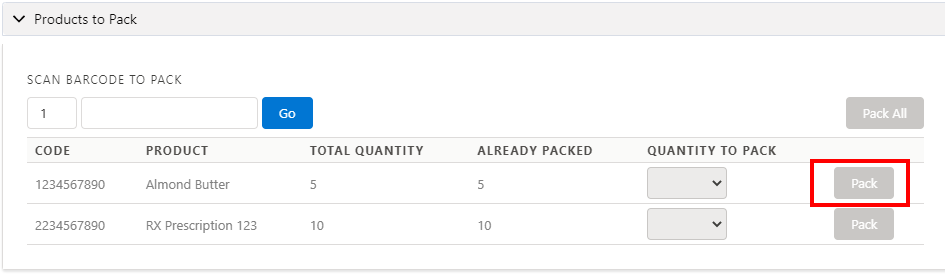
Don't worry if you have made a mistake in the number of products you have packed in a container, or if you have added the wrong type of container. Just use the "Delete" icons to remove the product / container.
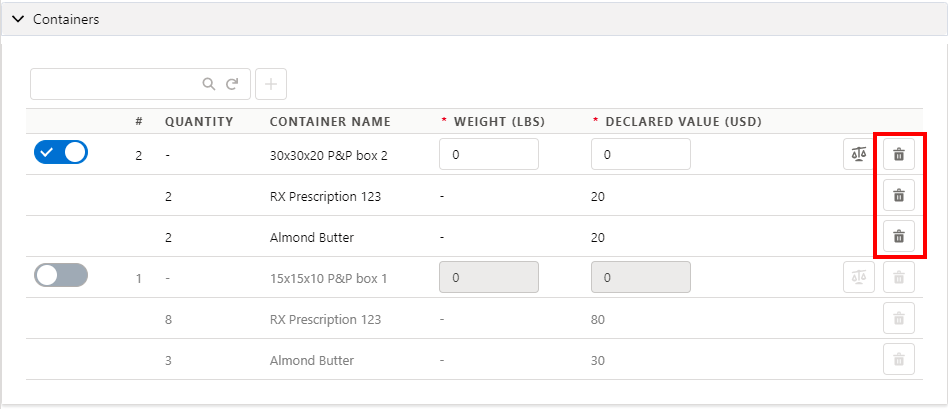
Once you have finished packing your products into the containers click on the "Ship" button.
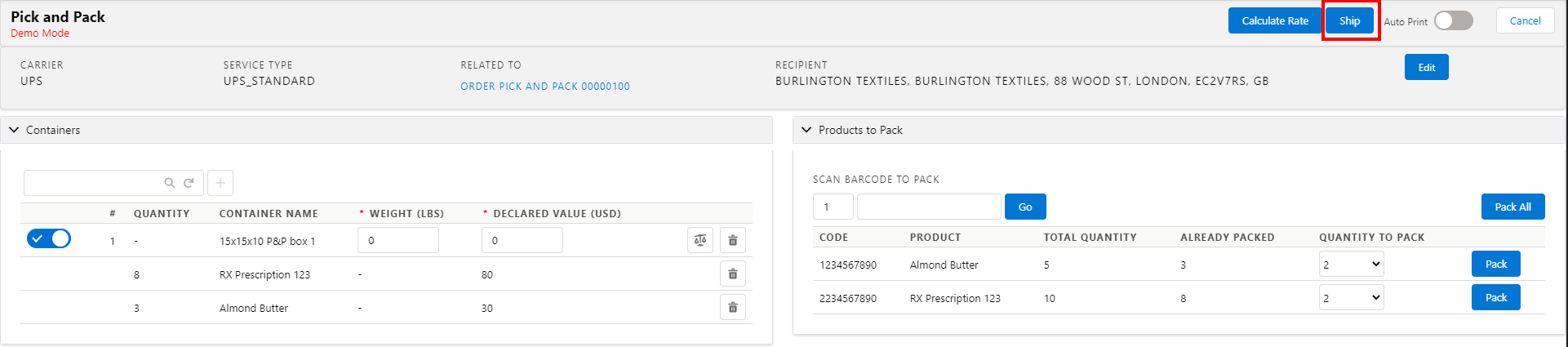
You can also Auto Print any of your shipping labels if you turn on Auto Print.
Your shipment will now have been created and your shipping labels will be ready to print (if you haven't already chosen "Auto Print").
If you look on the Shipment object you will see that we store all the information as to what was packed and which package its in:
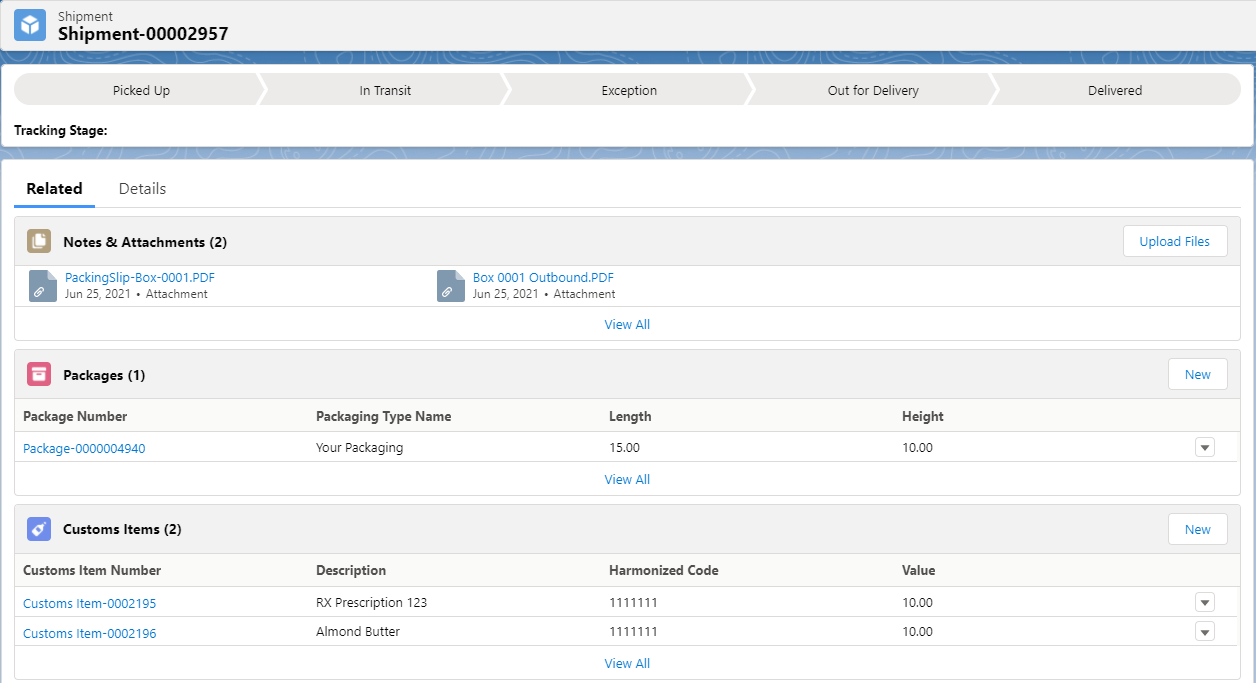